SMH Employs Innovative 3D Printing Technology to Help Overcome Pandemic-Related Supply Shortages
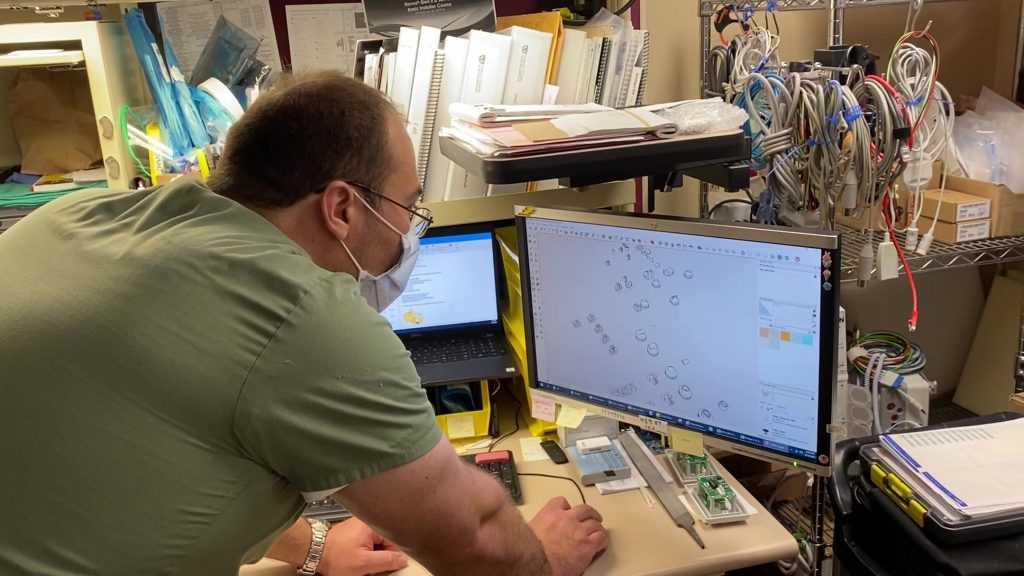
Across the nation, 3D printing has benefitted health care in multiple ways, including the creation of better performing medical devices and personalized care for patients. During the pandemic, SMH adopted a critical new use for the technology: safeguarding the personal protective equipment (PPE) that shields staff caring for COVID-19 patients.
During the first wave of the pandemic last year, one of the most valued pieces of PPE – controlled air-purifying respirators known as CAPRs – became scarce amid a worldwide shortage.
That’s when the SMH Biomedical Engineering team stepped in to help. Using a 3D printer, the team began producing a CAPR replacement part that manufacturers could no longer provide: a vital break-away tab for the helmet’s faceshields. Without it, the CAPRs could not be used.
“With PPE and other supplies critically low, it was an absolute necessity to do this – our clinical team needed those masks,” said Robert Santos, director of SMH’s Biomedical Engineering and Technology Assessment Department.
The Biomedical team’s efforts have been largely led by Biomedical Technician II Artem Chevtsov Before the pandemic, the department was not utilizing 3D printing. As the team faced continuing challenges from the disruption to traditional supply chains, Artem used his experience with 3D-printing technology to quickly set up a new printer and begin producing the CAPR replacement tabs out of a specialized plastic material. It was a great success story, as the 3D printed tabs not only helped ease supply shortages, but were found to actually work better than the original parts. Artem won Sarasota Memorial’s EXCEL Employee of the Month Award back in May for his resourcefulness and expertise.
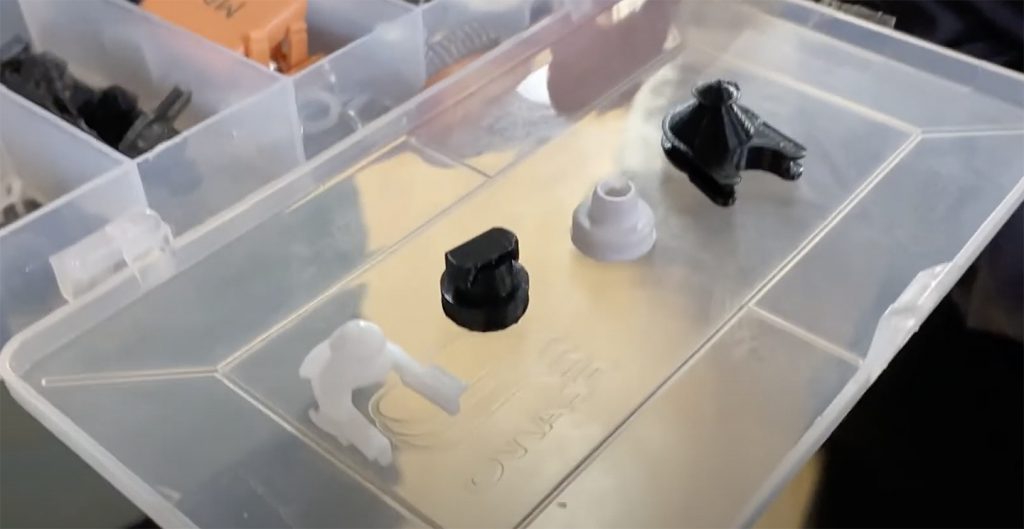
In the year since those first parts were 3D-printed at SMH, the team has begun printing more than a dozen other items that various hospital departments need to reinforce and protect equipment. The efforts have helped the hospital overcome supply shortages, saving time and money.
“We clearly cannot modify any medical device, and that’s not our intent, but if it’s a disposable item and helps protect our equipment, that’s where our focus is right now,” Robert explained.
Recently, SMH purchased a second, larger 3D printer to support the Bio-Med team’s innovative work.
“We’ve saved money from parts that were unavailable and have reduced damage to our equipment, but the real benefit is being able to quickly turn around those products and protective devices, and get them out to the clinicians,” Robert said.
For a video showing SMH’s 3D printer in action along with interviews with Robert and Artem, click here.